
After Hours Shipping

Real Time Order Tracking

Flexible Delivery Options
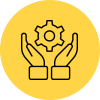
Basic Specifications | Input power | Single phase, 100 V | Single phase, 100 V to 115 V +10 % 50 Hz/60 Hz
–15 % |
||
Single phase, 200 V | Single phase, 200 V to 240 V +10 % 50 Hz/60 Hz
–15 % |
||||
3-phase, 200 V | 3-phase, 200 V to 240 V +10 % 50 Hz/60 Hz
–15 % |
||||
Environment |
Temperature |
Operating : 0 ˚C to 55 ˚C, Storage : –20 ˚C to 65 ˚C (Max.temperature guarantee 80 ˚C for 72 hours <Nomal temperature>) | |||
Humidity | Both operating and storage : 90 %RH or less (free from condensation) | ||||
Altitude | 1000 m or lower | ||||
Vibration | 5.88 m/s2 or less, 10 Hz to 60 Hz (No continuous use at resonance frequency) | ||||
Withstand voltage | Should be 1500 VAC (Sensed current: 20 mA) for 1 minute between Primary and Ground. | ||||
Control method | IGBT PWM Sinusoidal wave drive | ||||
Encoder feedback | 2500 P/r (10000 resolution) incremental encoder | ||||
Control signal | Input | 7 inputs (1) Servo-ON, (2) Alarm clear and other inputs vary depending on the control mode. | |||
Output |
4 outputs (1) Servo alarm, (2) Alarm,
(3) Release signal of external brake and other outputs vary depending on the control mode. |
||||
Pulse signal | Input | 2 inputs Supports both line driver I/F and open collector I/F. | |||
Output |
4 outputs Feed out the encoder pulse (A, B and Z-phase) in line driver.
Z-phase pulse is also feed out in open collector. |
||||
Communication function | RS232 | 1 : 1 communication to a host with RS232 interface is enabled. | |||
Display LED | (1) Status LED (STATUS), (2) Alarm code LED (ALM-CODE) | ||||
Regeneration | No built-in regenerative resistor (external resistor only) | ||||
Dynamic brake | Built-in | ||||
Control mode |
3 modes of (1) High-speed position control, (2) Internal velocity control and
(3) High-functionality positioning control are selectable with parameter. |
||||
Functions | Position control |
Control input |
(1) CW over-travel inhibition, (2) CCW over-travel inhibition, (3) Deviation counter clear,
(4) Gain switching, (5) Electronic gear switching |
||
Control output | (1) Positioning complete (In-position) | ||||
Pulse input | Max. command pulse frequency |
Line driver : 500 kpps, Open collector : 200 kpps |
|||
Type of input pulse train |
Differential input. Selectable with parameter, ((1) CW/CCW, (2) A and B-phase, (3) Command and Direction) | ||||
Electronic gear
(Division/Multiplication) of command pulse |
Setup of electronic gear ratio Setup range of (1-10000) × 2(0-17)/(1-10000) |
||||
Smoothing filter | Primary delay filter or FIR type filter is selectable to the command input. | ||||
Internal speed control |
Control input |
(1) CW over-travel inhibition, (2) CCW over-travel inhibition, (3) Selection 1 of internal command speed,
(4) Selection 2 of internal command speed, (5) Speed zero clamp |
|||
Control output | (1) Speed arrival (at-speed) | ||||
Internal speed command | Internal 4-speed is selectable with control input. | ||||
Soft-start/down function |
Individual setup of acceleration and deceleration are enabled, with 0 s to 10 s/1000 r/min. Sigmoid acceleration/deceleration is also enabled. | ||||
Zero-speed clamp | 0-clamp of internal speed command with speed zero clamp input is enabled. | ||||
Common | Auto-gain tuning |
Real-time |
Estimates the load inertia in real-time in actual operation and sets up the gain automatically corresponding to the machine stiffness. Useable at (1) High-response position control, (2) Internal speed control and (3) High-functionality position control. | ||
Normal mode |
Estimates the load inertia with an action command inside of the driver, and sets up the gain automatically corresponding to setup of the machine stiffness. Useable at (1) High-response position control, (2) Internal speed control and (3) High-functionality position control. | ||||
Masking of unnecessary input | Masking of the following input signal is enabled.
(1) Over-travel inhibition, (2) Speed zero clamp, (3) Torque limit switching |
||||
Division of encoder feedback pulse | 1 P/r to 2500 P/r (encoder pulses count is the max.). | ||||
Protective function | Hardware error | Over-voltage, under-voltage, over-speed over-load, over-heat, over-current and encoder error etc. | |||
Software error | Excess position deviation, command pulse division error, EEPROM error etc. | ||||
Traceability of alarm data | Traceable up to past 14 alarms including the present one. | ||||
Damping control function | Manual setup with parameter | ||||
Setup | Manual | Console | |||
Setup support software | PANATERM (Supporting OS : Windows98, Windows ME, Windows2000, and WindowsXP) |