
After Hours Shipping

Real Time Order Tracking

Flexible Delivery Options
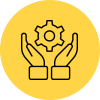
Schneider VFD Inverter Drive | ATV600 0.75-315KW
|
Mounting type | Cabinet integration |
Degree of protection | IP20 |
Power range for 50…60 Hz line supply
Three phase: 380…480 V (kW/HP) |
0.75…90/1…120 |
Three-phase: 400 V (kW) |
– |
Three-phase: 440 V (kW) |
– |
Three-phase: 480 V (HP) |
– |
Three-phase: 500 (kW) |
– |
Three-phase: 600 (HP) |
– |
Three-phase: 690 (kW) |
– |
Drive
Output frequency |
0.1… 500 Hz |
Control type
Asynchronous motor |
Standard constant torque, variable standard torque, optimized torque mode |
Synchronous motor | PM (permanent magnet) motor, synchronous reluctance motor |
Functions
Advanced functions |
Including all the advanced features of ATV600:
b Accurate measurement for monitoring system energy consumption (deviation < 5%) b Installation energy drift detection b Embedded Ethernet with direct access to system configuration and monitoring b Integration of actual pump curves to optimize the system operating point b Optimized pump monitoring based on actual operating point b Sensorless estimated flow rate b Measurements expressed in working units (e.g. m3/h, kWh/m3) b Limitation of overvoltage at the motor terminals b Contextual access to technical documentation through dynamic QR code b Continuous and historical real-time measurements with customizable dashboards b Predictive and preventive maintenance tracking functions (e.g. temperatures with PT100/1000 probe, fan monitoring) Easy setting of drive identification for Altivar Process Modular drives from 110 kW up to 800 kW (150…1100 HP) |
Integrated safety function |
1: STO (Safe Torque Off) SIL3 |
Number of preset speeds | 16 |
Number of integrated I/O
Analog inputs |
3: Configurable as voltage (0…10 V) or current (0-20 mA/4-20 mA), 2 of them including probes
(PTC, PT100, PT1000, or KTY84) |
Digital inputs | 6: Voltage 24 V c (positive or negative logic) |
Digital output | – |
Analog outputs | 2: Configurable as voltage (0…10 V) or current (0-20 mA) |
Relay outputs | 3: 1 with NO/NC contacts and 2 with NO contacts |
Safety function inputs | 2: For safety function STO |
I/O expansion modules (optional)
Analog inputs |
2 differential analog inputs configurable via software as voltage (0…±10 V) or
current (0-20 mA/ 4-20 mA), or for PTC, PT100, or PT1000, 2- or 3-wire |
Digital inputs | 6: Voltage 24 V c (positive or negative logic) |
Digital outputs | 2: Assignable |
Relay output module (optional)
Relay outputs
|
3: NO contacts |
Communication
Integrated |
Modbus/TCP, Modbus serial link |
Option modules |
Ethernet/IP, Modbus TCP and MD-Link dual port, CANopen Daisy chain, SUB-D and screw
terminal block, PROFINET, PROFIBUS DP V1, DeviceNet, BACnet MS/TP, POWERLINK |
Configuration and runtime tools | Graphic display terminal, embedded Web server, DTM (Device Type Manager), SoMove
software |
Standards and certifications | 86/188/EEC, IEC 61000-4-2, IEC 61000-4-3, IEC 61000-4-4, IEC 61000-4-5, IEC 61000-4-6,
EN/IEC 61800-3, EN/IEC 61800-5-1, IEC 61000-3-12, IEC 60721-3, IEC 61508, IEC 13849-1, TÜV certification, e marking |